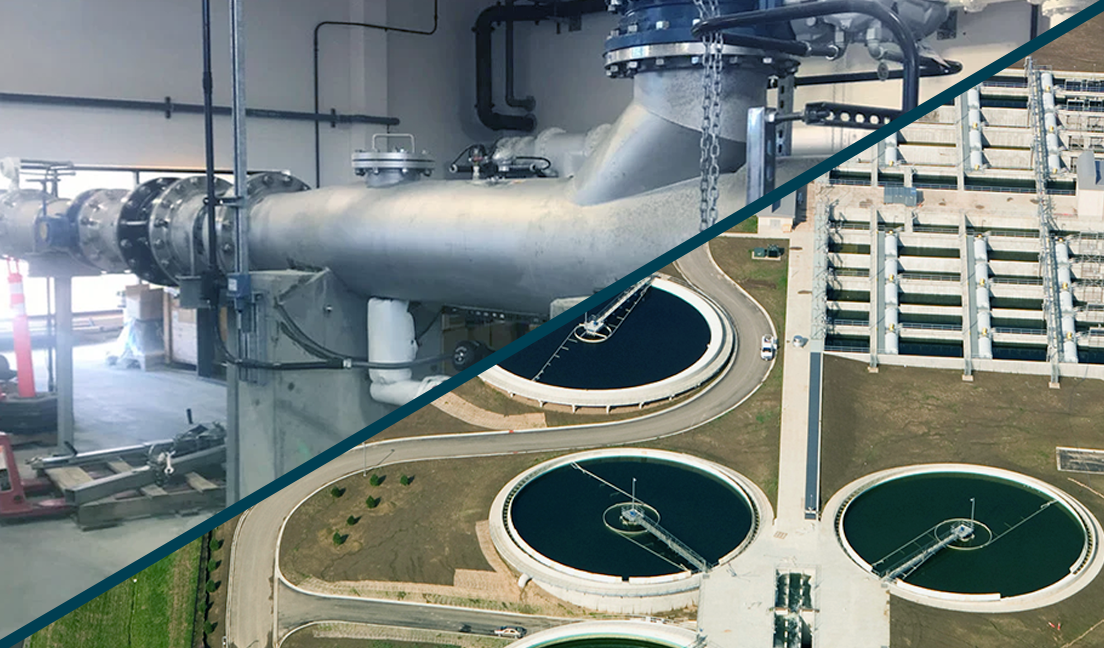
Ultraviolet (UV) disinfection is now a standard feature in most wastewater treatment systems. The technology is widely favored in wastewater treatment due to its non-chemical nature, no subsequent dechlorination process is required if there are effluent chlorine standards, and its ability to be unselective in disinfection performance. UV has also been embraced by the drinking water community as an effective barrier against chlorine tolerant organisms such as Cryptosporidium and Giardia.
While open channel has historically been the primary treatment technique, a more efficient approach is becoming widely deployed. Closed vessel UV systems provide a compelling alternative to open channel by containing the effluent in a pipe and thus delivering mutual benefits to the operators.
Closed vessel UV systems serve as the primary UV solution for various applications including drinking water, beverage and brewery, ultrapure water applications, aquatics, ballast water, surface and air, and aquifer storage and recovery wells. With over 1000 closed vessel UV systems in operation for wastewater disinfection, it is not a new or novel form of UV disinfection. Many configurations and lamp types are available, closed vessel UV systems can utilize horizontal or vertical lamps, medium pressure or low-pressure high output lamps supporting flows from a couple of gallons per minute up to more than 100 MGD. They provide reliable disinfection performance after all types of upstream processes—from lagoons to reverse osmosis. Enhancements in lamp technologies and reactor chamber designs have led to reduced lamp counts and optimized hydraulic behaviors both resulting into lower running costs and effort for the operators.
Delivering lowers costs and installation advantages
Traditionally open channel UV systems have been the preferred choice as they appear to be easily integrated into existing chlorine contact basins when wastewater treatment plants convert from chemical disinfection to UV. However, open channel UV systems depend heavily on precision alignment of poured concrete walls and floors that need to fit tight to the open channel system configuration. Therefore, significant construction is commonly required to make the UV system fit into existing chlorine contact basins.
Choosing closed chamber UV systems instead eliminates this work and translates to lower costs and easier, quicker installation. This facilitates even UV system installation during non-disinfection seasons in areas where this occurs.
Variable flange sizes and installation orientations in horizontal or vertical pipe runs provide design flexibility to easily fit the UV system into existing structures. The choice between a range of compact medium pressure in-line reactors and low-pressure high output reactors in L-shape flange arrangements allows closed vessel UV systems to be installed into virtually any existing site, even including footprint constrained arrangements.
Like open channel UV systems, the closed reactor setups can be gravity fed and don’t require additional pumps. Particularly the low lamp count requirement of medium pressure UV reactors makes them favorable in sites where available head is limiting the choice for an appropriate UV systems.
For low pressure UV systems, lamp count is as well significantly reduced by use of long lasting high output 800-watt amalgam UV lamps, featured in Evoqua’s UVLW systems. These systems require significantly less lamps compared to other closed reactor or open channel systems using conventional low pressure high output lamps (up to 320 W per lamp). Additionally, these lamps allow for energy efficient operation due to their broad dim-range of 30 -100% power.
Particularly small wastewater treatment sites can leverage significant benefit from choosing closed reactor UV systems in terms of significantly reduced consumable components, simplified installation and footprint, minimization of components as compared to open channel systems.
Evoqua’s closed vessel UV systems offer the fewest number of lamps in one of the smallest footprints currently available in the UV market. Illustrated below is an installation example that was originally designed around open channel but switched to closed vessel when the original bid went overbudget. In addition to capital cost savings, operational costs including power, lamps, quartz, power supplies, and maintenance can be 15% -20% less when compared to traditional open channel systems.
Example Savings Analysis
Closed Vessel |
vs. |
Open Channel |
||
---|---|---|---|---|
![]() |
Footprint | |||
New build vs. retrofit | Retrofit into existing building | vs. | New structure | |
Space requirements | 6’ long x 7.5’ wide | vs. | 20’ long x 8’ wide | |
![]() |
Lamp Requirements | |||
Number of lamps | 12 MP lamps | vs. | 48 LPHO lamps | |
Load requirements | Total load 15 kW | vs. | Total load 7.5 kW | |
![]() |
Total Costs | |||
Installation costs | 2-2.5x UV Cost | vs. | 3-6x UV Cost | |
Capital costs (UV + installation) | $369,000 | vs. | $450,000 |
Lower maintenance and easier component access
When choosing the most appropriate UV solution for a wastewater site, maintenance requirements are often a decisive factor for the operators and maintenance staff. Not only lamp replacement cycles need to be considered in this respect, but additional maintenance requirements caused by e.g. potential algae growth as well.. Within a short period of time, algae can grow in open channel UV systems adhering to the concrete walls due to slow moving water, food source, and direct exposure to sunlight. Eventually the algae can slough off leading to elevated coliform levels. Therefore, additional time and effort might be required to remove algae from the channel walls on a regular basis. Finally, the presence of algae can impact hydraulics and transmittance.
Because there is no open water in closed UV vessels, algae growth is less of concern. Therefore, reduced maintenance time will be required as compared to open channel systems. Easy access to internal parts of the chamber also makes maintenance simple, particularly when the reactor features an access hatch. This allows for easy internal inspection to remove debris or to add acid if chemical cleaning is required.
UV systems in wastewater applications typically feature automatic wiping systems to continuously keep the quartz clean. With its wiping mechanism and fractional horsepower motor mounted externally to the chamber, closed vessel systems also facilitate ease of routine maintenance and inspection. This does as well apply for any routine lamp replacement which is clean and simple to execute this way. For open channel UV systems lamp cables and connectors may be located in the effluent which leaves them prone to algae growth, water ingress, and cumbersome regular replacement procedures.
Additional maintenance benefits of Evoqua’s closed vessel UV systems include:
- Wiper rings are easily replaced as they are a one-piece ring that can be accessed through the access hatch
- Reduced power consumption and extended lamp life by using electronic ballasts that automatically adjust the power to the lamps based on flowrate and lamp intensity to minimize energy consumption
- Increased disinfection efficiency
- Reduced maintenance time because of reduced consumable components
- Automatic mechanical wiper for self-cleaning of the quartz and UV sensor
- Reductions in corrosion and structural damages because of the wastewater being contained in pipe and UV chamber
Improved reliability and safety along with reduced risk for operators
In open channel UV system designs, water level control is key to meet the desired disinfection performance. While various gate options including fixed serpentine weirs or sliding gates are available to be installed at the channel outlet, they all require additional attention from the operators. Adjusting gates such as sliding or counter-weighted gate systems require frequent hinge lubrication and often struggle to meet height tolerances. Furthermore, they could be prone to blockage and wear in case of frequent flow rate variations. On the other hand, fixed weir designs are typically designed for peak flow conditions. Thus they may require significant space and may lead to undesirable low water levels during most common low and average flow conditions.
The closed vessel approach requires a completely filled UV reactor. Typically, this can be achieved by providing the effluent water level higher than the chamber (normally through effluent piping), making any additional gates and corresponding costs, time and effort obsolete.
With regards to safety and health aspects, a persuasive case can be made for closed vessel UV system installations, which prevents the operator from exposure to the wastewater and UV light. There are numerous safety benefits associated with keeping UV operations contained in a closed vessel system, primarily the prevention of UV light which can burn exposed skin in seconds. Burns to the inside of the eyeball, sometimes called arc eye or welding flash, can also occur and are extremely painful.
Additional benefits of the closed vessel system include no risk of lost/damaged tools or cell phones because there’s no open water surface where they can be accidentally dropped into the channel. There’s also reduced inhalation risk of wastewater aerosols and bug nuisance due to the closed nature of the system.
In summary, it can be concluded that there are good reasons to consider closed vessel UV systems as a superior disinfection alternative to open channel UV systems, particularly for sites treating flow rates of 5 MGD or less, which represents about 80% of US wastewater treatment plants. However, the closed vessel UV approach should also be considered for those plants larger than 5 MGD as the benefits described throughout the article are applicable in all flow scenarios. The example below describes operators’ experiences operating both open channel and closed vessel UV systems.
Realizing the benefits of closed vessel UV at Indiana municipal wastewater facility
The City of Scottsburg, IN—located between Indianapolis, IN and Louisville, KY—is home to approximately 7,000 people. To disinfect the municipal wastewater before discharge, the city selected to install Evoqua’s ETS-UV™ system. The staff had been previously operating an open channel UV system at other facilities which made them well-versed in the differences in system design.
The UV reactor is fabricated from 316L stainless steel and contains an automated wiper system that reduced quartz fouling. The chamber also features an access hatch that makes routine maintenance much easier and more convenient for operators. Each chamber contains medium pressure lamps, which can be removed with effluent in the UV chamber. The lamps use the Twist-LOK™ lamp connector for ease of connection. Municipal plants like Scottsburg that only disinfect seasonally can often achieve two years of lamp life.
When asked about the new closed vessel system, the Scottsburg facility manager stated, “We have been impressed with the ease of use of the closed vessel UV system. The automatic wipers keep the quartz sleeves clean without constant manual cleaning and overall, the installation is cleaner and much more compact. The units are installed in a building with climate control making it easy to service the unit or change lamps in a matter of minutes, keeping our employees safe and out of the weather. Water level control issues have been designed out and we appreciated the improved safety that these modern systems provide to the plant staff.”